Every ceramic artist knows the magic of a perfect black stain Pottery . It’s all about the mix of metal oxides and clay. This mix creates stunning depth and texture.
Black ceramic stains are more than just colors. They open doors to artistic expression. Whether you’re experienced or new, learning the best cone 10 black stain recipes can make your work stand out.
Great ceramic stains come from the right mix of chemistry and technique. Today, artists have more color options than ever. This makes it easier to get rich, consistent black colors.
Exploring black stain pottery opens up new techniques. You’ll learn to turn simple clay into dramatic art. From old Iron Oxide recipes to new commercial stains, there’s a lot to discover.
Knowing how to use ceramic stains is key. They’re added at 5-8% in glazes and 15-25% in clay bodies. This skill lets you bring your ideas to life.
Understanding the Chemistry Behind Cone 10 Black Stains
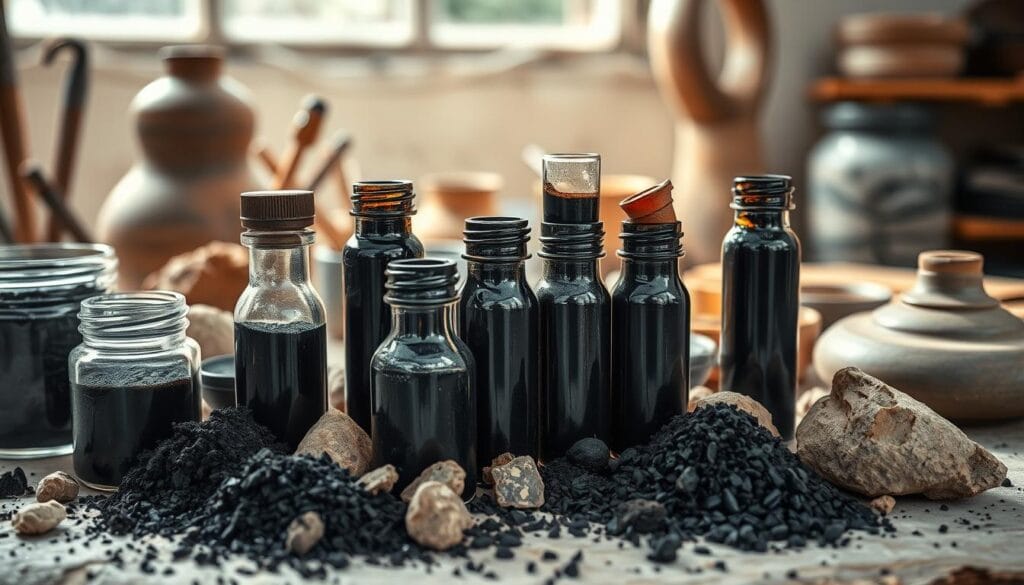
Exploring how to make ceramic stains for pottery leads to a deep dive into black stain chemistry. Ceramic materials are complex systems of chemical interactions. These interactions change during the firing process, especially at cone 10 firing temperature.
Black stain chemistry is about finding the right balance of ceramic oxides. These oxides interact at high temperatures. The mix needs precise chemical compositions for a deep black color and finish.
Ceramic Oxides and Their Roles
Different ceramic oxides are key in making black stains:
- Metal oxides like iron, manganese, and copper
- Flux materials that help lower melting points
- Stabilizing compounds that enhance color durability
Temperature Requirements and Effects
At cone 10 firing temperature (about 2350°F), ceramic oxides change a lot. The extreme heat causes chemical reactions that develop the characteristic black pigmentation.
Chemical Reactions During Firing
The firing process triggers complex molecular interactions. Ceramic oxides melt, combine, and create new chemical structures. These structures determine the final stain color, texture, and durability.
Understanding these chemical processes helps potters make consistent, high-quality black stains for their ceramic projects.
Essential Materials and Equipment for Black Stain Making
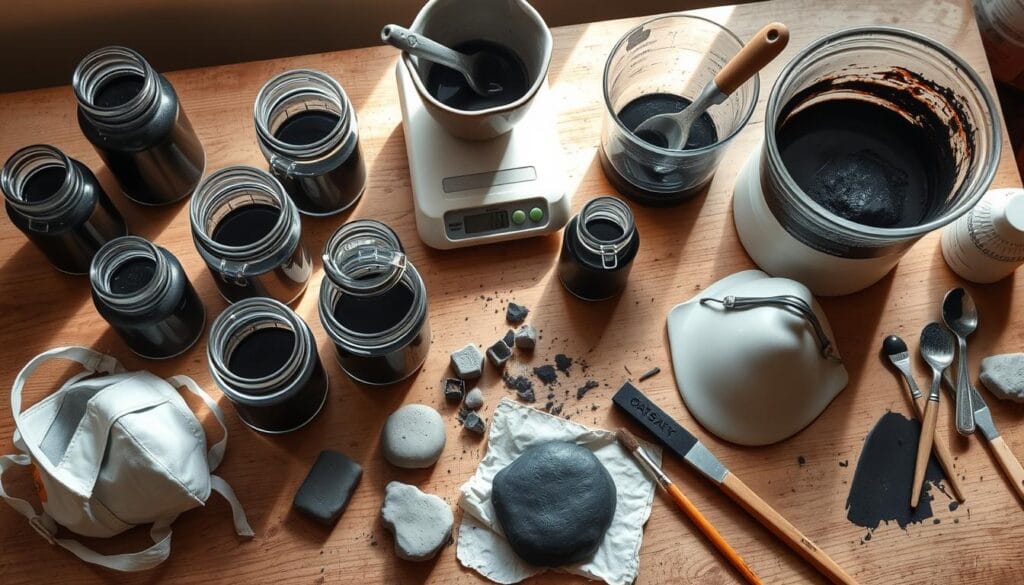
Making professional black stains for pottery needs the right materials and tools. You must know the best ingredients and equipment for top-notch black stains.
- Metal oxides (iron oxide, manganese dioxide)
- Copper carbonate
- High-temperature ceramic mixing containers
- Precision weighing scales
- Protective safety gear
Choosing the right pottery equipment is key for making stains. Look for tools that help mix and prepare better:
- Cone 10 capable kiln
- Ball mill for thorough ingredient blending
- Airtight storage containers
- Heat-resistant mixing tools
How you mix can affect your stain’s quality. Manual mixing is good for small batches, but ball mills are better for big ones.
Material | Recommended Percentage | Temperature Tolerance |
---|---|---|
Iron Oxide | 40-50% | Up to 2350°F |
Manganese Dioxide | 30-40% | Up to 2200°F |
Copper Carbonate | 10-20% | Up to 2100°F |
Always keep safety first when working with ceramic stains. Wear the right gear and make sure your area is well-ventilated.
Best Cone 10 Black Stain Recipe Pottery: Traditional Formulas
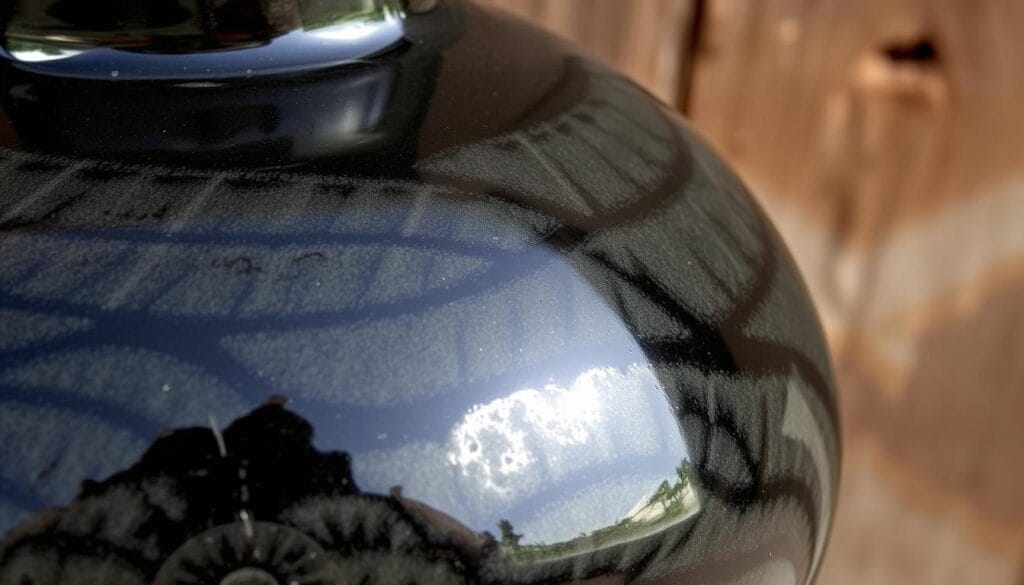
Making the perfect black glaze for cone 10 pottery is all about metal oxide stains. Ceramic artists use special techniques to get deep, rich black colors. They mix chemicals in just the right way.
Looking into traditional black stain Pottery recipes shows the beauty of ceramic color. The right mix of metal oxides can make your pottery look amazing. It creates stunning deep black finishes that grab people’s attention.
Iron Oxide-Based Recipes
Iron oxide is key for making black stains for cone 10 ceramics. Recipes use specific amounts to get the best results:
- Black Iron Oxide: 85-90% concentration
- Manganese Dioxide: 5-10% for depth
- Cobalt Oxide: 1-3% for intense black tone
Manganese Dioxide Variations
Manganese dioxide gives ceramic artists different black stain options. It lets them play with black colors in unique ways:
Ingredient | Percentage | Effect |
---|---|---|
Manganese Dioxide | 75% | Deep charcoal black |
Black Iron Oxide | 15% | Enhanced darkness |
Cobalt Oxide | 5% | Rich undertone |
Copper Carbonate Combinations
Copper carbonate adds special touches to black stains. It makes the colors deeper and more complex when used right.
Trying out these traditional black stain recipes helps you find your own style. But remember, the firing atmosphere and clay type also affect the color.
Modern Commercial Stain Alternatives
Pottery artists now have exciting options with modern commercial ceramic stains. These pre-mixed black stains offer consistent and stable colorants. They make the ceramic creation process simpler. Mason stain products have changed how potters apply colors.
Commercial ceramic stains offer many benefits for both professional and hobby potters:
- Consistent color reproduction
- Reduced experimental time
- Safer material handling
- Wide range of color options
When choosing pre-mixed black stain Pottery , consider these important factors:
- Firing temperature compatibility
- Desired color intensity
- Cost-effectiveness
- Manufacturer reputation
Leading manufacturers like Mason Color Works have developed advanced stain technologies. These technologies help potters get predictable results. While commercial stains might cost more than traditional raw oxide recipes, they save a lot of time in testing and color development.
Stain Type | Price Range | Color Consistency |
---|---|---|
Mason Black Stains | $15-$35 per pound | High |
Raw Oxide Mixtures | $5-$20 per pound | Variable |
Professional potters love the predictability and convenience of commercial ceramic stains. They allow more time for artistic expression and less for complex chemical formulations.
Preparation Techniques for Superior Results
To get amazing black stain Pottery results on ceramics, you need to prepare well and use the right techniques. It’s all about knowing how to apply ceramic stain and mix black stain.
Surface Treatment Methods
Getting your ceramic surface ready is key for the best stain results. Make sure your bisque-fired surface is clean and dust-free. Here’s what to do:
- Thoroughly clean the ceramic surface with a soft, lint-free cloth
- Gently sand any uneven areas to create a smooth base
- Wipe down with alcohol to remove any residual oils
Mixing Guidelines
When mixing mason stain with glaze, follow these tips:
Material Type | Stain Percentage | Application Recommendation |
---|---|---|
Glazes | 5-8% | Smooth, even coverage |
Slips | 15-25% | Rich, intense coloration |
Clay Bodies | 15-25% | Deep, consistent color |
Application Tools and Processes
Choose the best way to apply your ceramic stain. Experts suggest:
- Brushing for detailed, controlled application
- Spraying for uniform, thin layers
- Dipping for complete, consistent coverage
Pro tip: Always weigh ingredients precisely and mix thoroughly to prevent sedimentation. This ensures your black stain ceramic work looks even and has the right texture.
Firing Considerations and Atmosphere Control
Mastering cone 10 firing needs a deep understanding of firing atmospheres. These atmospheres greatly affect black stains. The look of your pottery depends a lot on the firing environment you create.
Different firing atmospheres change how black stains look:
- Oxidation firing makes lighter, more muted black tones
- Reduction firing creates rich, deep black colors with complex undertones
- Controlling temperature is key for consistent results
With reduction firing, managing oxygen levels is crucial. The chemical reactions between stain ingredients and kiln atmosphere can change your ceramic’s look a lot. Oxygen reduction creates unique chemical reactions that enhance black stain depth and complexity.
For successful cone 10 firing, consider these:
- Choose clay body right for the firing atmosphere
- Pick black stain recipes for the firing conditions
- Watch kiln temperature closely
- Try different atmospheric conditions
Professional potters suggest keeping firing schedules consistent and documenting your process. Each firing is a chance to improve your technique. It helps you see how oxidation and reduction environments affect black stains.
Troubleshooting Common Black Stain Issues
Ceramic artists often face challenges with black stains in pottery. Knowing how to fix black stain problems can make your ceramic pieces look better.
Fixing ceramic stain problems needs a careful plan. We’ll look at common issues you might run into while making pottery.
Color Inconsistencies
Color issues can be a big problem for potters. To get consistent black stain, try these tips:
- Thoroughly mix your stain before application
- Use consistent application techniques
- Apply stain in thin, even layers
- Test firing temperatures carefully
Surface Defects
Issues like pinholing or flaking can ruin your ceramic’s look and strength. These problems often come from:
- Incorrect application thickness
- Inadequate stain component integration
- Uneven surface preparation
Defect Type | Potential Cause | Solution |
---|---|---|
Pinholing | Thick stain application | Apply thinner, more even layers |
Flaking | Poor surface preparation | Ensure clean, properly prepared surface |
Mottling | Uneven firing atmosphere | Control kiln environment |
Application Problems
Getting black stain right takes skill and attention to detail. Focus on your technique, materials, and firing conditions to avoid problems.
Pro tip: Small batch testing can help you refine your technique before committing to larger ceramic projects.
Advanced Application Methods for Black Stains
Exploring advanced black stain techniques can make your ceramic work stand out. Ceramic artists can take their work to the next level by mastering complex stain layering. This creates depth and visual interest.
Professional potters suggest several innovative ways to apply black stains:
- Try multi-layered stain techniques
- Use black stains with other colors
- Apply stains to textured surfaces
- Use resist methods for detailed designs
Understanding different application strategies can greatly improve your black stain technique. Textural variations are key to unique ceramic decorations. Artists use techniques like:
- Sgraffito
- Wax resist
- Controlled gradient applications
Stain layering needs precision and careful temperature control. Commercial ceramic artists often test different firing atmospheres for nuanced black tones. Your experiments with application densities can lead to stunning visual effects, making your work unique.
Safety Measures and Best Practices
Working with pottery stains and materials needs careful safety steps. Protecting yourself and your workspace is key. This means paying close attention to detail and following safety rules.
In a pottery studio, your safety comes first. Professional ceramic artists know how to keep their work area safe. They aim to avoid health risks.
Protective Equipment Requirements
- Wear a high-quality respirator to prevent inhalation of ceramic dust
- Use chemical-resistant gloves during stain preparation
- Always wear safety glasses or protective eyewear
- Use long-sleeved clothing to minimize skin exposure
Workspace Ventilation
Good ventilation in a pottery studio is crucial. It keeps the air clean by moving out harmful particles. This makes your work area safer.
Ventilation Strategy | Recommended Action |
---|---|
Air Filtration | Use HEPA-rated air purifiers |
Workspace Layout | Position work areas near windows or exhaust systems |
Dust Control | Wet cleaning methods to minimize airborne particles |
Material Storage Guidelines
Storing stains right is important for keeping them good and safe. Here’s how to store ceramic stains:
- Use airtight containers with secure lids
- Keep stains in a cool, dry location
- Label containers with precise content and date of acquisition
- Separate potentially reactive materials
Remember, handling and storing ceramic materials carefully can lower health risks. It also makes your supplies last longer.
Converting Recipes Between Different Cone Temperatures
Changing a cone 10 glaze to cone 6 needs careful chemical knowledge and precise tweaks. Your glaze recipe conversion is more than just changing numbers. It’s about making strategic changes to keep the look and function you want.
When you’re converting glaze recipes, keep these important points in mind:
- Flux material composition
- Melting point modifications
- Thermal expansion properties
- Color development potential
The secret to successful cone temperature changes is knowing how different ceramic oxides work at different firing temperatures. Lower temperature glazes often need more flux materials to melt right.
Cone Temperature | Flux Adjustment Strategy | Typical Material Changes |
---|---|---|
Cone 10 to Cone 6 | Increase low-temperature fluxes | Add Frit 3134, reduce refractory materials |
Cone 6 to Cone 10 | Increase high-temperature stabilizers | Add silica, reduce low-melting fluxes |
Here are some practical tips for glaze recipe conversion:
- Start with base recipe modifications
- Test small batches extensively
- Document each experimental variation
- Analyze fired results critically
Remember, successful cone temperature adjustments take patience and precision. Each glaze recipe has its own challenges. So, thorough testing is key to getting the ceramic finish you want.
Environmental Considerations and Sustainable Practices
In pottery, going green is key. As a ceramic artist, you can help the planet by choosing eco-friendly ways to create. Start by picking materials wisely and cutting down on waste.
Here are some ways to make pottery more sustainable:
- Recycle clay using new methods like pugmill reclamation
- Use safe, natural colors instead of harmful ones
- Measure materials carefully to avoid waste
- Try plant-based and recycled colors
By making smart choices, your studio can be kinder to the environment. Mason stains are a great choice for their vibrant colors and low waste. They’re perfect for artists who care about the planet.
Today’s ceramic artists are finding new ways to make stains that are better for the earth. By picking the right materials and improving how you work, you can lessen your impact. Look into new color sources and try out green ways to color ceramics.
The future of ceramics is all about being green and keeping it that way. Your choices in materials, waste, and how you make things can help make ceramics better for the planet.
Conclusion
Your journey into ceramic stain techniques shows the amazing depth of black stain pottery. It’s not just about following a recipe; it’s about expressing your art and always learning. Now, tools like Procreate help you design detailed stencils, and new ceramic tech opens up more creative paths.
Pottery innovation has changed how artists work, letting them try new colors and firing methods. Knowing about chemical reactions, surface treatments, and materials is key to making great black stain ceramics. By trying out different oxides, firing conditions, and ways to apply stains, you’ll get better and better.
As you grow in your ceramic art, remember that each piece has its own story. Whether you make useful items or art pieces, improving your stain techniques will make you stand out. Keep learning, be bold in your experiments, and always explore new things in black stain pottery.